Advanced Global Platform for a Large Manufacturer of Industrial Lubricants
Full-Scale Enterprise Quality Management System for a Global Tobacco Producer
We built a full-scale quality management system that completely digitized the production and supply chain procedures of a global tobacco manufacturer.
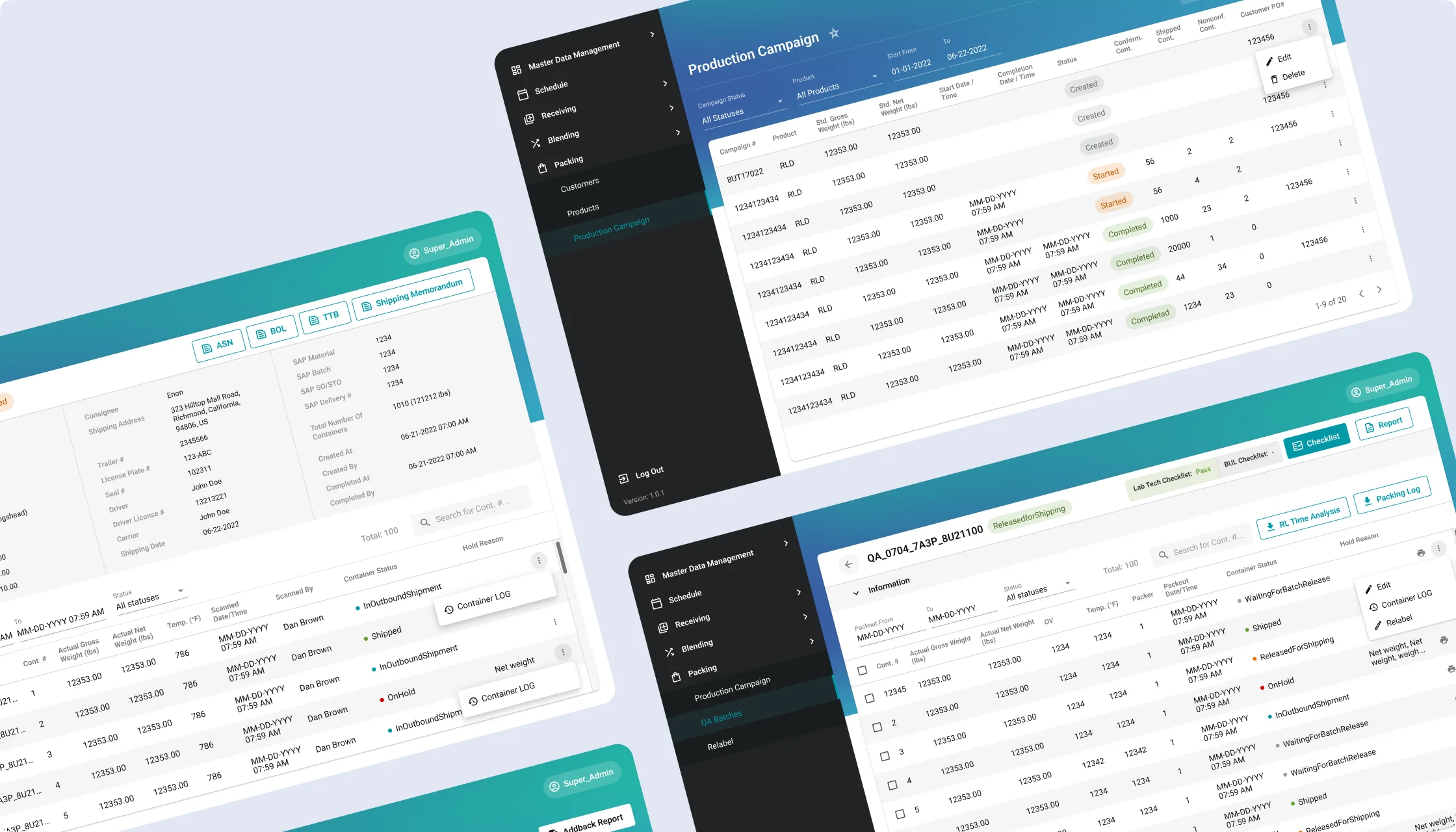
Background
A leading global tobacco manufacturer sought to digitally transform and automate its production processes and establish consistent quality control at each step. Their production and supply chain workflows were fragmented and involved tons of paper-based documentation. Having to deal with paper record-keeping in reports and supporting documents, the client often failed to promptly respond to any sudden changes (such as equipment breakdowns, environmental conditions, workers’ performance, etc.) and deviations in this complex production process. This negatively affected the quality of finished (blended) products and resulted in financial losses.
The client needed a centralized information management solution that would allow them to ensure consistent quality control through the entire cycle: receiving, lab testing, blending, production, batching, and shipping.
Challenge
Paper-based workflows
The client scheduled all their planned production and shipping campaigns for the year and stored them in their internal database.
When they received raw materials for tobacco production, they had to manually complete the necessary paper documents with receipt details, i.e., time of receipt, quantity of material received, etc. Additionally, they had to manually compare the amount with the planned one. This process took too long, and they had to deal with substantial paperwork to complete and store. Paperwork had to be maintained at each stage of production, where documentation was kept during process checks (products' quantity, quality, and conditions).
Lack of quality control
From raw materials’ procurement and lab trials to production, batching, and shipment, the client needed to control the quality and conditions of each step of this complex process. Yet, they had to deal with paper-based documents and ‘raw’ data collected from IoT devices, whose output format took time to read and interpret.
Additionally, changing factors like temperature conditions, workers’ productivity, and equipment breakdowns required them to act immediately, which often was not possible.
Inconsistent data management
Based on the formulas and receipts prepared at the laboratory testing stage, the client mixed the materials in the required proportions to produce the finished mixture (product). The process was complicated because they had to create supporting documentation detailing the materials needed, their amounts, and the requirements for the end product in the form of a pull sheet for each production run.
Additionally, the client’s system collected the blending conditions data (temperature, weight, moisture, etc.) from the IoT sensors at the blending stage. They didn’t have a universal method of storing, managing, transferring, and extracting this data for further analytics.
Lack of a single database
The finished (blended) product was put into the container and processed for transportation. At transportation, the client’s system received the products’ conditions data from IoT sensors, yet these records were scattered; they lacked a single database solution to store documents in a single location to make further work with them easy and efficient.
Methodology & Approach
Based on the client’s defined challenges, we set the following goals:
- Provide a dedicated planner tool from which the client could automatically manage their campaigns (including lab trials, production runs, shipments, repairs, relabeling, and others) by scheduling specific actions to be executed in the set time.
- Build a unified database that would integrate with the client's software and hardware and take relevant data from these sources in real-time.
- Establish end-to-end quality control throughout the entire process, including procurement, blending, lab testing, packing, and shipment, by providing dedicated monitoring and reporting functionality.
- Provide the possibility to evaluate employees’ performance in real-time to make the necessary process adjustments and optimizations with productivity tracking tools.
Every complex process starts with simple solutions. Understanding this, we first provided an MVP, which was a simple SQL database that we used to collect and store data from the client’s enterprise management system. We periodically took data, such as trial test results, raw materials’ conditions during blending, finished products’ conditions during containers’ validation and transportation, and other data collected from IoT devices from the system’s FTP servers and manually uploaded it into SQL.
The choice of SQL as a centralized database solution allowed us to test different scenarios of centralized data management (data capturing, sending, editing, transferring, analytics, parsing, and more) and document workflow digitization in optimal, cost-efficient conditions. At this point, we could define the scenarios that proved to be the most efficient for continuous quality control through each process step and make informed decisions to implement them in a full-scale solution.
During the project, we adopted an agile and flexible methodology, ensuring adaptability to the client’s requirements and enterprise workflows at every stage of the development process. By maintaining close collaboration with the client and providing regular process updates, we delivered a full-scale enterprise quality management platform that seamlessly integrated into the client’s established workflows (the existing ERP system).
Solution
In due time, we delivered a full-scale quality management solution that streamlined the entire production and logistics process with a versatile functionality set.
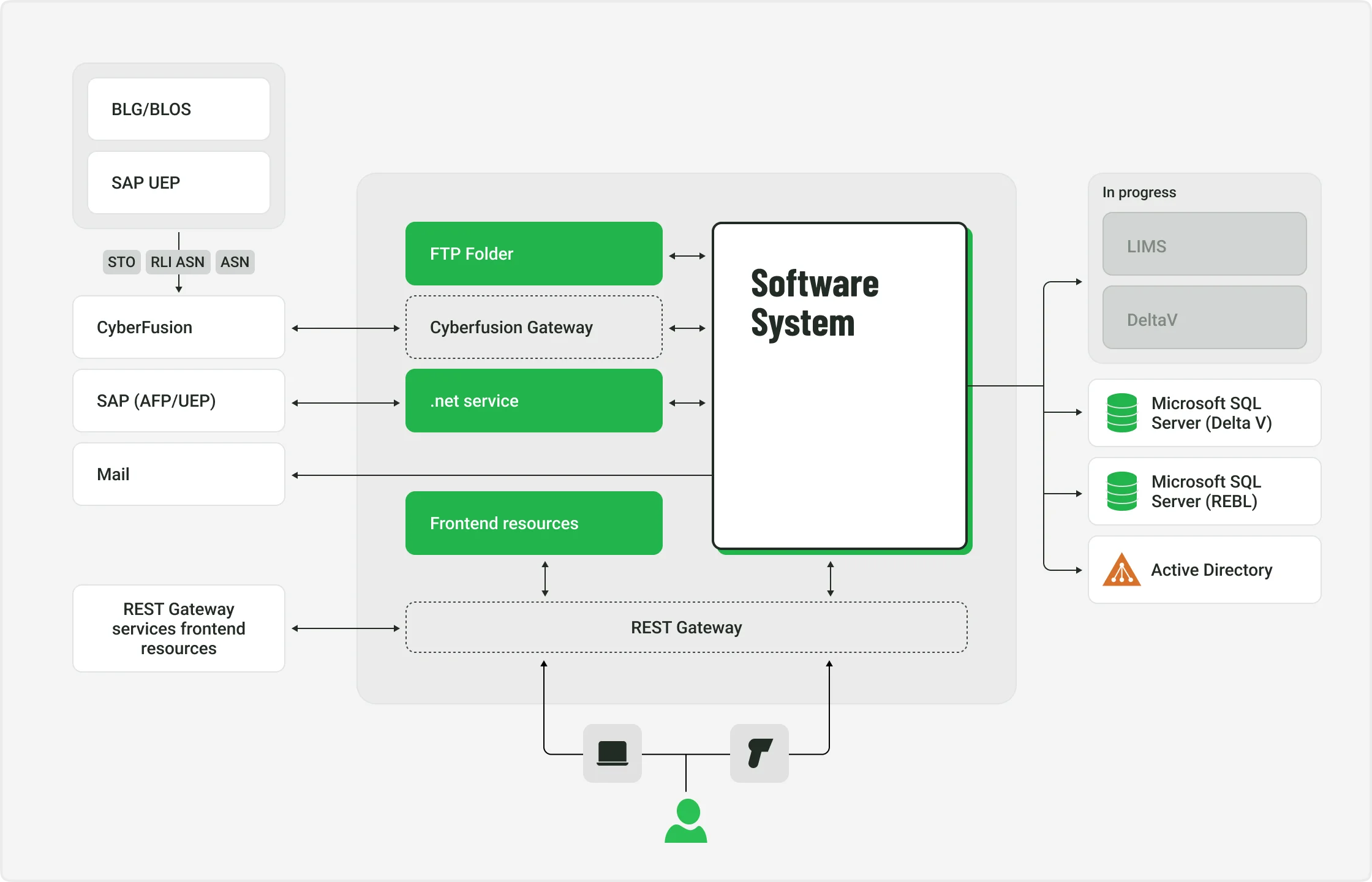
Intelligent production planning tool
First, we built an intelligent production planning tool as an automated calendar that collected data (raw materials, trials, blended products, shifts, workers, etc.) from the client’s file with the campaign schedules. The tool enabled the following:
- Instant campaign creation: Users can create a single or multiple campaigns with a button click.
- Convenient data grouping and sorting: Users can sort data on campaigns by week, month, or year to quickly assess and evaluate the working efficiency over particular periods for data-driven performance, conditions, or quantity analytics and reporting.
- Integration with IoT scanners: When scanning raw materials at receiving, blended products at packing, and containers with approved products at shipping, the IoT scanners automatically connect to the planner to check that the data they obtain during scanning matches the data they obtained during scanning.
- Integration with the hardware printing tool: The operator can schedule document and label printing for particular campaigns and dates.
- Transparent data tracking: Detailed logs present all changes the operator makes with data in a history log view.
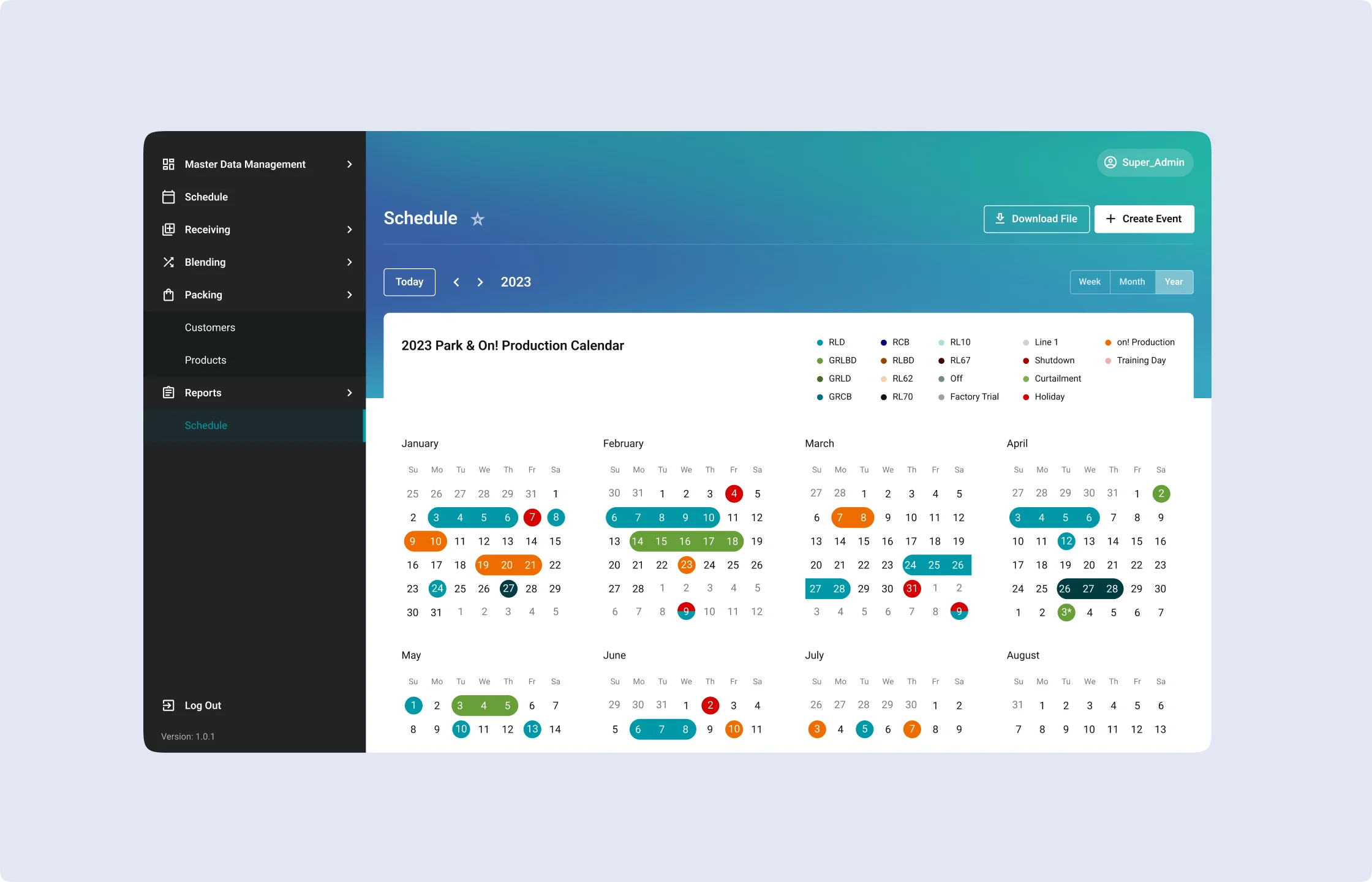
Real-time data management system
Within the platform, we provided a unified database that continuously integrated with the client’s system and collected data in real-time. We were able to automate and centralize data transfer and distribution processes and streamline document workflows by replacing paper-based documentation with digital documents.
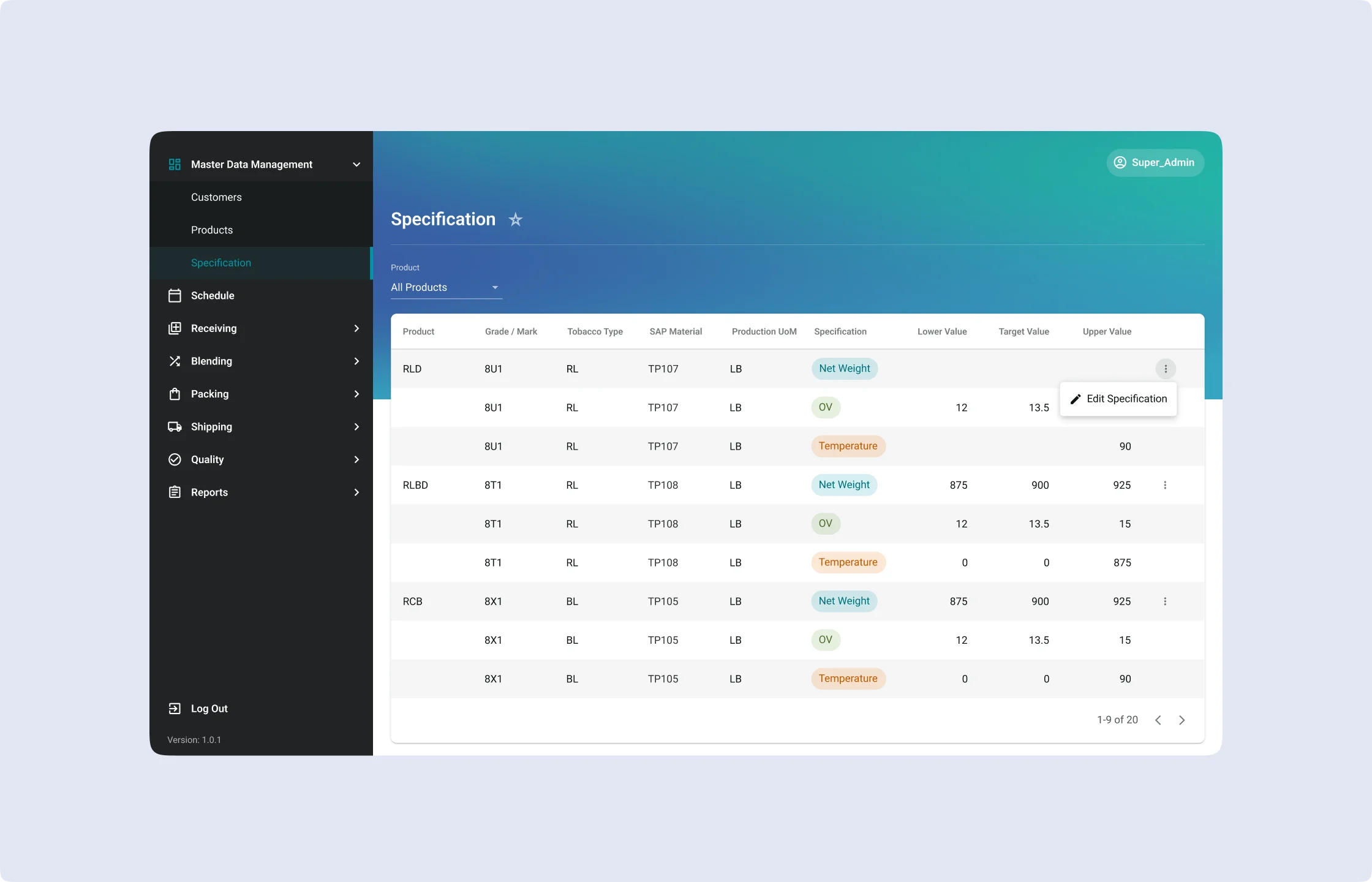
IoT-powered integrations
We enhanced the capabilities of our quality management platform by integrating it with the client’s IoT scanners and sensors. The client used them throughout the entire production and logistics cycle, as they allowed them to automate the following procedures:
- Verify that the amount of raw materials received matches the amount initially planned (in the production planner).
- Control the quality of the finished (blended) products by verifying that the conditions measured during blending match the pre-defined threshold values. The ones that deviated from those values were sent for additional validation. The ones that matched were marked as ready for production.
- Gather employee and equipment performance data from sensors in the working zones to control the operational productivity of every worker and each asset in real-time and proactively estimate their resulting efficiency within the production campaign (production run).
- Collect conditions data at the shipment stage from the products ready for production and create supporting documentation to store in the provided data management system.

Smart employee tracking & productivity management app
We provided a dedicated app that enables the client to efficiently manage manpower throughout the entire process. The app provided detailed, real-time analytics on hours worked per employee, the number of employees per shift, production results per shift, employee attendance, and other data. With this app, the client can promptly evaluate each employee’s efficiency and plan shifts that are more data-driven by making the necessary adjustments to these shifts (add or remove workers from the shift, move workers between shifts, change the timing or duration of a shift, and more).
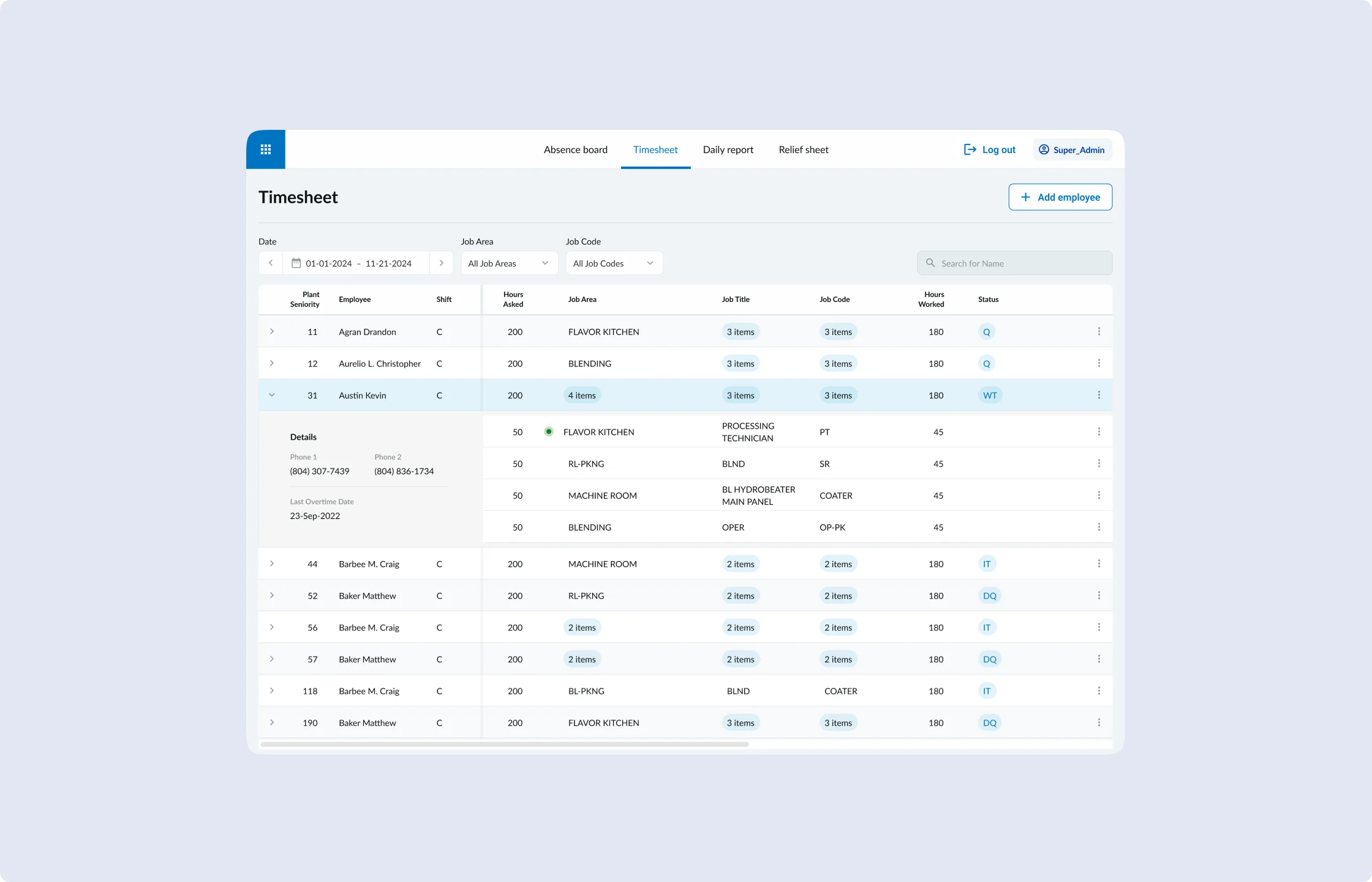
Automated reporting
We established consistent quality and quantity control at different stages of the production and logistics processes, with automated generation of the following types of reports:
- Trials reports
We integrated the solution with the client’s laboratory software, which collected conditions data on raw materials’ blending trials and tests and generated detailed reports in a readable format from that data. With these reports, the client could efficiently control the trial procedures by tracking chemical tests in real-time, which enabled informed and prompt decision-making on which trials were successful and which were not.
- Blend deviation report
This report type was composed of data on raw materials’ condition deviations from the set threshold value, collected during the blending process. With it, the client could continuously evaluate and control the quality of blending procedures and promptly discontinue or adjust running blending campaigns.
- Production campaign report
Data on the conditions of the blended products was retrieved from their containers by scanning them after blending. The report facilitated quality management of ready products, promptly ‘sorting out’ the ones that didn't comply with the quality standards set.
- Final product reportData on the blended products approved for further production, including the number of products produced and the number of shifts taken to produce that amount. In this way, the client could promptly monitor the output production results by evaluating if the production KPIs were met and making informed decisions on what should be changed during the next production run.
- Hold report
The report contains all data on the ‘wrong’ products (the ones with deviations) that were put on hold for further actions (dispositions) required.
- Disposition reportThis report type collects all the previously ‘held’ products with dispositions (actions) assigned to each one.
- Released products reportThe ‘wrong’ products that were earlier dispositioned are then added to this report.
- Addback reportOperators may decide to add some containers marked as the bad ones (for any deviation reason) during the previous production campaign to the current production campaign (if they produce the same product).
- Waste report
The reports contain all the products that don’t match the quality requirements set and can’t be ‘dispositioned’ (i.e., they go to waste).
In this way, we ensured operative data retrieval and collection, and provided consistent process quality control through the procurement, packing, and shipping stages.
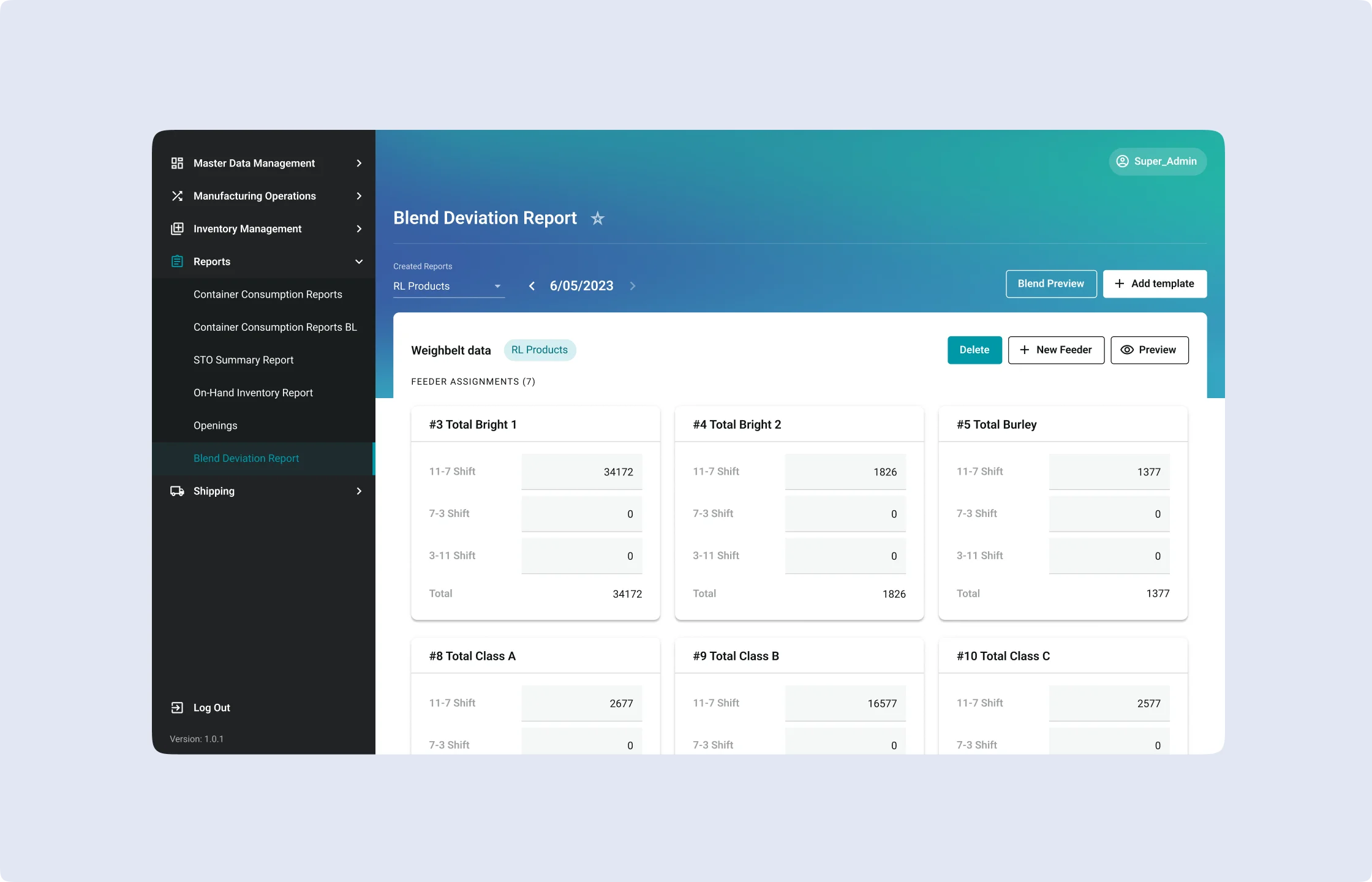
Smart relabel campaign management tools
If the data printed on a particular product’s label was incorrect, the operator could send it to a relabel campaign via the dedicated module that automated the whole procedure. The operator initiated the campaign and sent the correct label data to the system. The system then saved the updated data to the database and sent a command to the connected label-printing hardware.
Once the new label was printed, the assigned operator scanned it with their IoT-connected equipment to check if the data printed matched the one in the database.
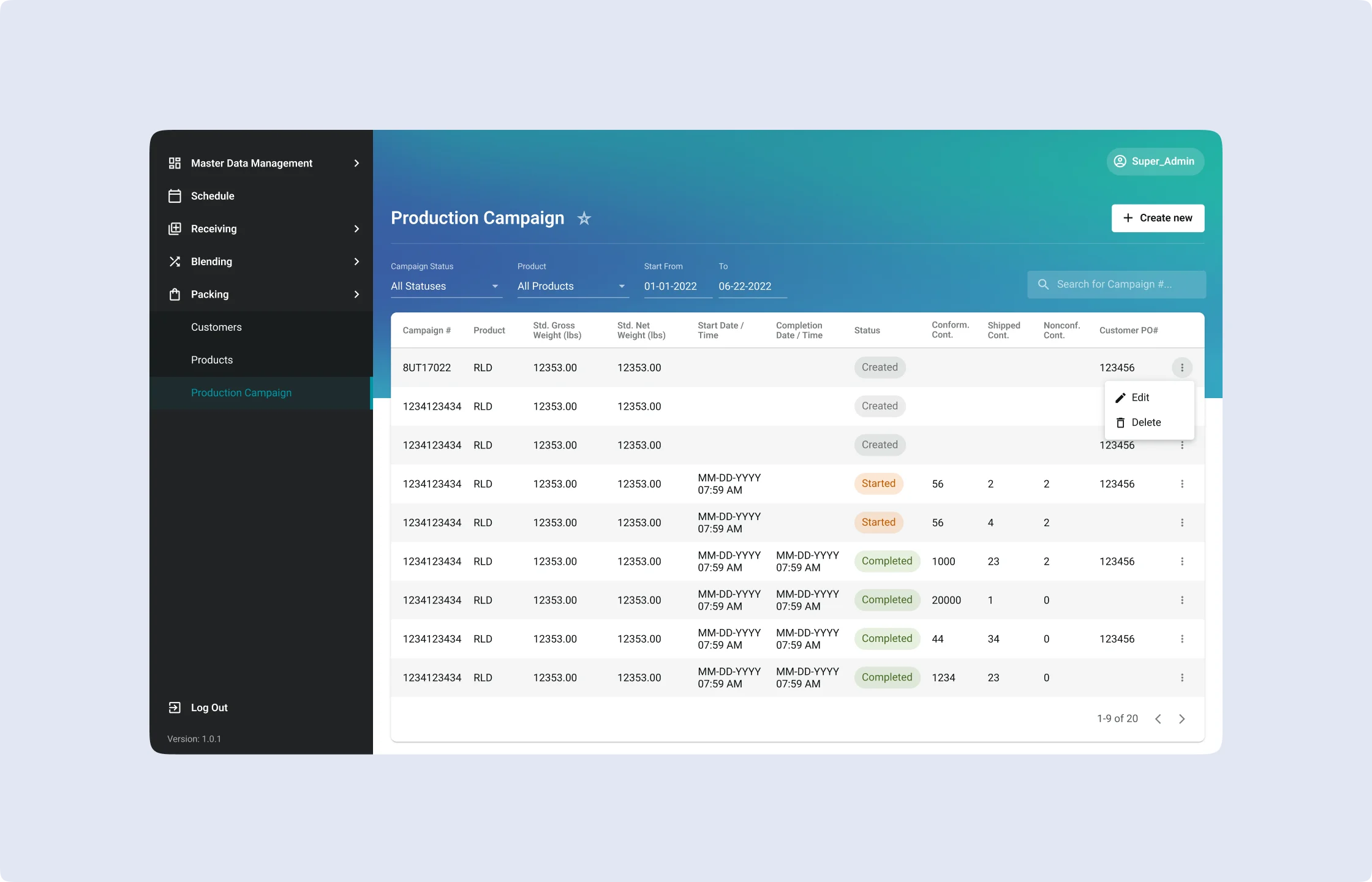
Technology Stack
Project Results
We provided the client with a comprehensive production quality management platform that allowed them to automate tobacco production workflows end-to-end, from lab testing and procurement to production and distribution, which resulted in optimized labor input, accelerated production time, and reduced operational costs.
In particular, the client managed to:
- Streamline production planning procedures with faster campaign creation, real-time data validation, event scheduling, and detailed activity logs, which reduced manual efforts and ensured continuous process transparency.
- Accelerate document workflows throughout production by moving all paper-based documentation to digital. As a result, the client could accomplish each production stage much faster than before and save on paperwork costs.
- Enhance quality control at the procurement, production, and shipment stages, which significantly reduced the amount of products of inferior quality as well as production costs.
- Improve the overall employee productivity with a dedicated app that enabled real-time work analytics per shift and allowed for more rational labor distribution between shifts, allowing avoiding employees’ overtimes and burnout.
The development of an extensive sales analytics platform with a variety of modules aimed at facilitating the work of distributors and maximizing their performance.
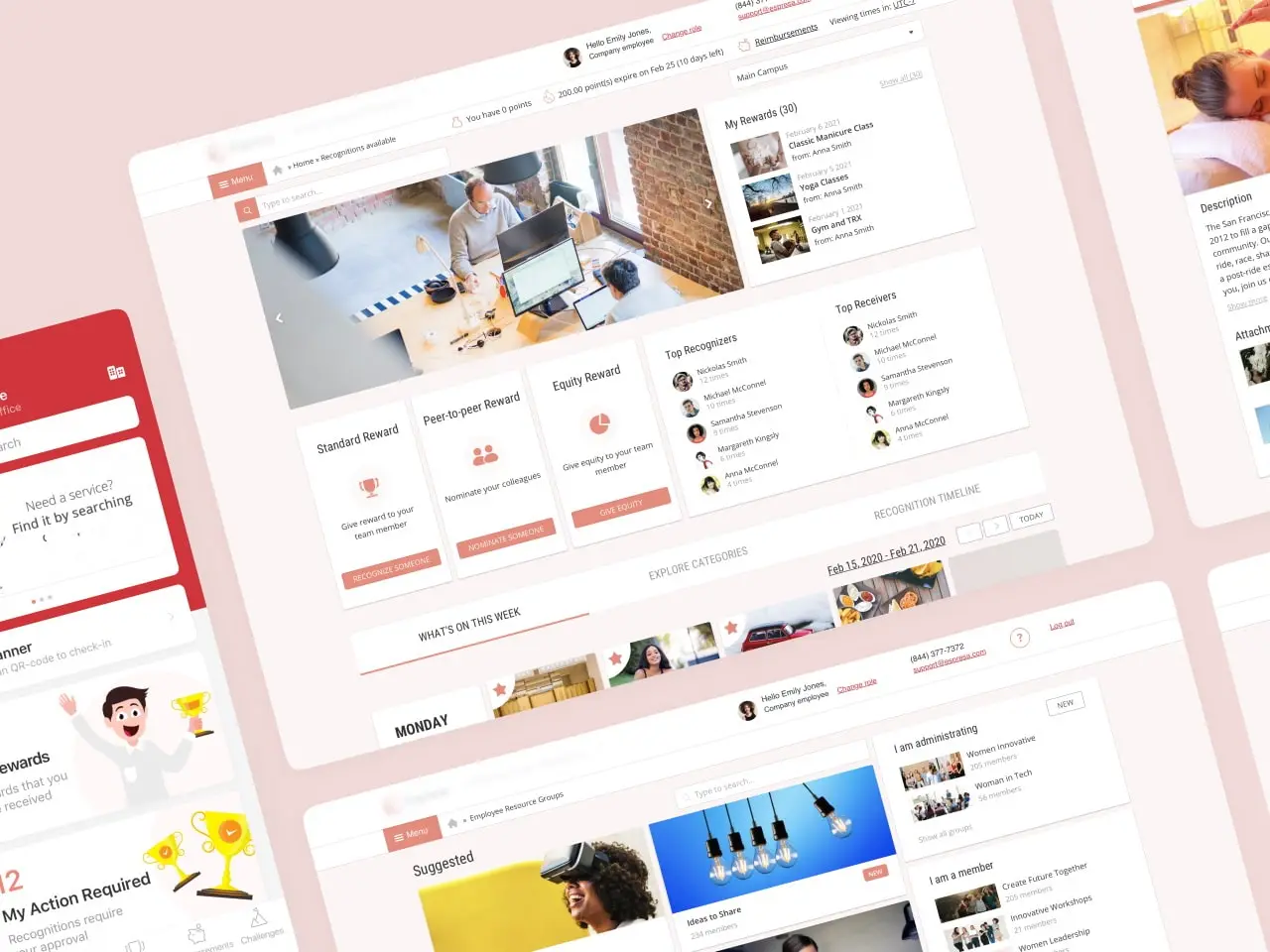
A culture benefits platform delivering an immersive employer experience, contributing to better recognition of HR work, and improving the overall company’s image.